Propiedades y aplicaciones de aleación de MG-Re-ZN-ZR
Según los principios de aleación, ND entre los elementos de tierras raras (RE) exhibe una solubilidad relativamente alta en MG, contribuyendo significativamente tanto a la temperatura ambiente como a la fuerza de alta temperatura. RE mixtos (predominantemente CE) y CE muestran la solubilidad más baja (0.85%), lo que beneficia la resistencia a la alta temperatura, pero afecta negativamente la resistencia y la plasticidad de la temperatura ambiente. LA tiene el efecto más débil, ofreciendo contribuciones inferiores a la fuerza de alta y baja temperatura en comparación con ND y CE.
ZM3 y ZM4 pertenecen al sistema MG-CE. Ambas aleaciones comparten contenidos idénticos de re (ricos en CE) y Zr (ver la tabla a continuación) pero difieren en el contenido de Zn: ZM3 tiene Zn baja (0.2%–0.7%), lo que resulta en una menor resistencia a la temperatura ambiente, mientras que ZM4 contiene Zn más alta, mejora la resistencia a la temperatura ambiente pero reduce la resistencia a la temperatura alta. Ambas aleaciones exhiben una excelente estabilidad térmica a 200–250 ° C, con ZM3 manteniendo una resistencia casi sin cambios de hasta 250 ° C. La microestructura de las aleaciones MG-CE consiste en compuestos α-fase y RE en los límites de grano. El tamaño del grano disminuye al aumentar el contenido de Zr disuelto, mejorando las propiedades de temperatura ambiente. Para cumplir con los requisitos de rendimiento estandarizados, el ZR disuelto debe ser ≥0.4% para ZM3 y ≥0.5% para ZM4 (diámetro de grano promedio ≤0.04 mm).
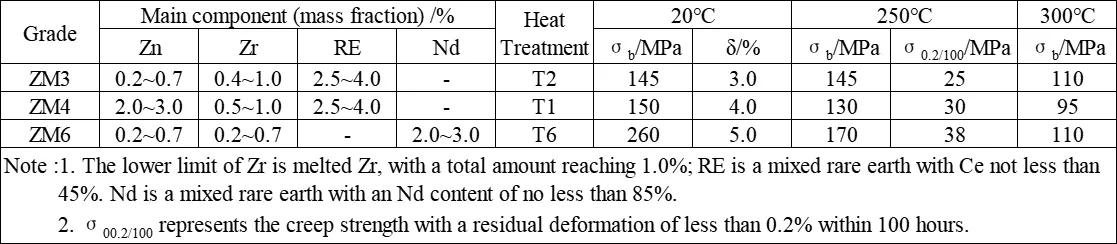
La composición química y las propiedades mecánicas a temperaturas altas y bajas de las aleaciones de magnesio resistentes al calor
I. Composición química y propiedades de la aleación ZM3

Composición química y contenido de impurezas (%en peso) de ZM3
El sistema de tratamiento térmico de la aleación ZM3: ZM3 se usa típicamente en el estado de talla. Cuando se recocido, el proceso recomendado es (325 ± 5) ° C durante 3–5 h, seguido de enfriamiento por aire. La temperatura de encendido de ZM3 en el aire es ≥400 ° C, aunque la inflamabilidad depende de las dimensiones y la geometría de la parte. Las partículas finas o el polvo se encienden fácilmente, mientras que los chips mecanizados representan riesgos de fuego más bajos a menos que se calienten por encima de los puntos de encendido. Las secciones gruesas requieren calentamiento prolongado a la combustible.
II. Proceso de fusión y fundición de aleación ZM3
(1) La aleación se derrite en un crisol de acero bajo en carbono para soldar. El proceso de fusión de las aleaciones que contienen circonio es diferente del de las aleaciones de magnesio que contienen aluminio. Debe llevarse a cabo en el mismo crisol que el casting. Transferir a otro crisol para la fundición causará pérdida de contenido de circonio. La aleación se derrite debajo de la cubierta de un flujo compuesto de cloruros y fluoruros. Durante el proceso de aleación, los metales de tierras raras no deben expuestos a altas temperaturas en el aire sobre la superficie líquida, y no deben retirarse de la superficie del líquido para evitar la oxidación y la pérdida. La pérdida de zinc se puede ignorar, mientras que la pérdida de tierras raras varía según la operación de fundición, que generalmente varía del 10% al 15%. El circonio se agrega en forma de una aleación maestra de magnesio-circonio con una fracción de masa de circonio superior al 25%. Durante el refinación, se rocía un flujo especial sin cloruro de magnesio sobre la superficie del metal. Esto se debe a que el cloruro de magnesio en los flujos ordinarios reaccionará con metales de tierras raras para formar cloruros de tierras raras que precipitan del líquido metálico, causando la pérdida de tierras raras. Antes de fundir, el metal se deja reposar durante 15 a 20 minutos para permitir que el flujo se separe del metal y precipite con compuestos insolubles. Luego, la temperatura se reduce al nivel requerido para fundir las fundiciones. Al menos del 15% al 20% de la fusión de la aleación debe permanecer en el fondo del crisol para evitar la escoria, el flujo y el circonio insoluble que se vierte en el molde.
(2) Durante el proceso de preparación de la aleación, se debe prevenir la contaminación por elementos como aluminio, hierro, silicio y manganeso, ya que estos elementos obstaculizan el efecto de refinamiento de grano del circonio.
(3) Debido a la baja solubilidad del circonio y su tendencia a formar compuestos con varios elementos de impureza y perderse, la cantidad de circonio agregada debe ser de 3 a 5 veces el contenido de circonio requerido en la aleación.
(4) El grado de refinamiento de grano está estrechamente relacionado con el contenido de circonio disuelto en la aleación. Al mismo tiempo, el contenido de circonio tiene un impacto significativo en las propiedades de tracción de la aleación. Por lo tanto, la tecnología de fusión y el control de la temperatura son extremadamente crucial.
Iii. Propiedades físicas de la aleación ZM3
La aleación ZM3 no es magnética. Su rango de temperatura de fusión es 590 - 645 ℃. La conductividad térmica λ es 117 W/cm · ℃ a 100 - 300 ℃. La densidad γ es 1.80 g/cm³. La resistividad ρ a 20 ℃ es 73 nΩ · m. La capacidad de calor específica y el coeficiente de expansión lineal de la aleación ZM3 se muestran en la siguiente tabla.

El coeficiente de expansión lineal de la aleación ZM3

La capacidad de calor específica de la aleación ZM3
La microestructura de la aleación ZM3 en la condición AS-CAST consiste en una solución sólida Mg y compuestos bloqueados distribuidos en los límites del grano. En casos de corrosión profunda, se puede observar la segregación intragranular de Zr. Un mayor contenido de ZR conduce al tamaño de grano más fino de la aleación y una tendencia menor para que se formen compuestos dentro de las dendritas. Después de recocer a 325 ° C durante 3 a 5 horas, algunos compuestos precipitan como pequeñas partículas dentro de los granos. La aleación de magnesio ZM3 tiene una excelente resistencia a la corrosión en el aire seco, pero su estabilidad química es pobre en el aire húmedo, el agua (especialmente el agua de mar) y reacciona vigorosamente con la mayoría de los ácidos inorgánicos. En las atmósferas industriales, la resistencia a la corrosión del magnesio es similar a la del acero de carbono medio. La película de óxido de magnesio no es densa, por lo que el tratamiento de la superficie es necesaria para el uso a largo plazo en condiciones atmosféricas. Las aleaciones de magnesio son estables contra el ácido selénico, los fluoruros y el ácido hidrofluorico, formando sales insoluble. A diferencia del aluminio, las aleaciones de magnesio no reaccionan con hidróxido de sodio y también son estables en gasolina, queroseno y aceite lubricante. El magnesio es uno de los metales más electronegativos y no debe ensamblarse directamente con piezas hechas de aleaciones de aluminio (excepto aleaciones de Al-MG), aleaciones de cobre o acero, ya que esto puede causar corrosión electroquímica. El hierro, el cobre, el níquel, el silicio, los cloruros y otras impurezas, así como ciertos defectos de fundición, pueden reducir la estabilidad de corrosión de las aleaciones de magnesio. Zr en la aleación puede refinar el tamaño del grano y eliminar los efectos nocivos de las impurezas, mejorando significativamente la resistencia a la corrosión de la aleación.
IV. Propiedades de proceso de aleación ZM3
(1) Formando el rendimiento.
La aleación ZM3 tiene una excelente procesabilidad de fundición, con una temperatura de fundición de 720 a 800 ° C. La aleación tiene buenas propiedades de llenado, y su fluidez, medida por la longitud de la barra de prueba de fundición, es de 300 mm. No hay tendencia a formar porosidad microscópica durante la solidificación. La primera grieta en la prueba de tendencia de grietas térmicas se forma en un ancho de anillo de 12.5 a 15 mm. La tasa de contracción lineal es del 1.3%.

Propiedades de tracción típicas de las fundiciones de aleación de ZM3 a temperatura ambiente y alta temperatura
(2) rendimiento de soldadura.
La aleación puede ser soldada por soldadura por arco de argón y tiene un buen rendimiento de soldadura de reparación. El estrés interno debe eliminarse después de la soldadura, y la calidad interna y la inspección de grietas superficiales deben llevarse a cabo después de la soldadura.
(3) Proceso de tratamiento térmico
La aleación solo se recoce cuando sea necesario.
(4) Proceso de tratamiento de superficie
La superficie de la fundición debe oxidarse químicamente para formar una capa protectora delgada. Antes del tratamiento con oxidación química, la fundición debe ser arenada y desengrasada. Según los diferentes usos de las piezas, la protección del aceite o la pintura debe llevarse a cabo después del tratamiento con oxidación.
(5) Rendimiento de mecanizado y molienda
La aleación tiene un excelente rendimiento de mecanizado y se puede mecanizar a una profundidad de corte mayor y una velocidad muy alta en comparación con otros metales. La potencia requerida para eliminar una cierta cantidad de metal es menor que la de cualquier otro metal. Durante el mecanizado, se pueden obtener excelentes superficies lisas sin moler o pulir, ya sea con o sin cortar líquido.
V. Aplicaciones de la aleación ZM3
La aleación ZM3 se usa ampliamente en piezas del motor, accesorios y varias cubiertas.